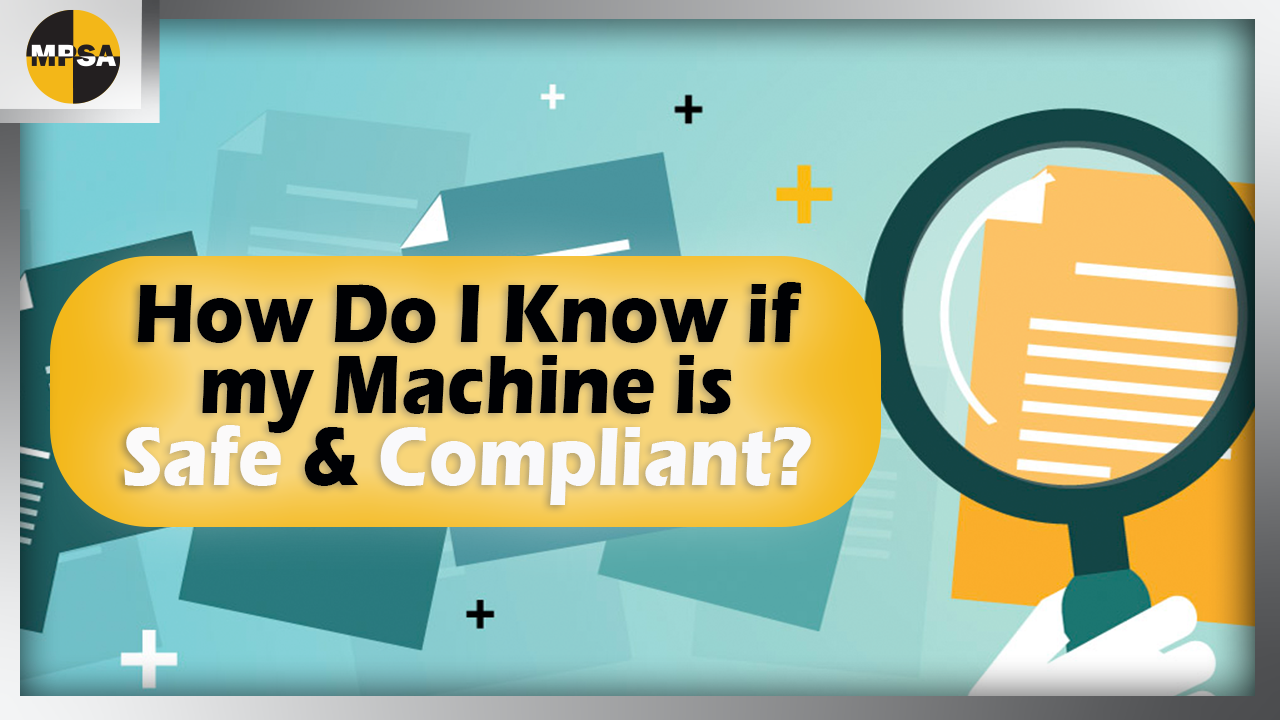
How Do I know If My Machine is Safe and Compliant?
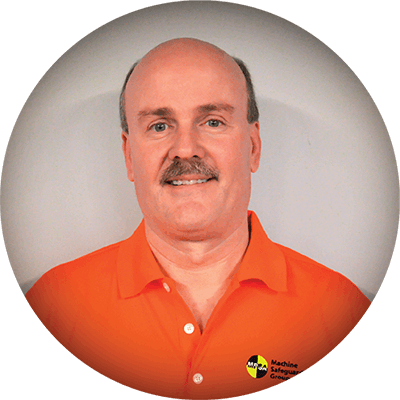
Posted By: David Kerr
February 22nd, 2022
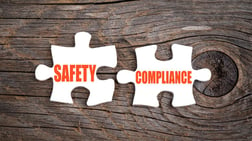
Today I'm guiding you through our process on how to answer two questions that every industrial machine owner should ask themselves:
Is my machine safe? Is my machine compliant with required safety standards?
Skip to a Section:
Starting Note | Step 1: Identification | Step 2: Documentation | Step 3: Review | Step 4: Discussion | Contact MPSA
Watch the on-demand webinar recording
A note before we begin...
Before starting, I want to emphasize that a compliant and safe machine requires careful and disciplined assessment, design, engineering, installation, and validation by qualified machine safety personnel. MPSA defines qualified machine safety personnel as certified machinery safety experts (CMSE).
So, if you hesitate about this information and have to ask, then the answer is probably no; your machine is not compliant with machine standards or might not be safe. Unfortunately, these questions are often only asked after a close call or, worse, following a machine safety incident.
So let’s go step by step to learn how to know if your machine is safe and compliant before disaster strikes.
Step One: Identify Your In-House Machine Safety Team
First and foremost, you need to identify your in-house machine safety stakeholders. These stakeholders may look different for each facility but typically include operations, EH&S, engineering, maintenance, quality, and automation or instrumentation. This team will be essential for completing the subsequent steps on this list.
Step Two: Collect Essential Documentation
Secondly, identify your device and machine safety documentation. Many organizations often keep an engineering library where records live for the life of the machinery.
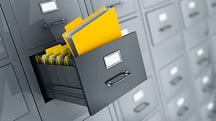
You’ll need; accent and closed call reports, operating instructions and maintenance requirements, risk assessments, lockout, tag out, HCC procedures, OAM documents, management change records, and safe distance calculations.
Other documents like the machine safety risk assessment are an individual risk assessment, explicitly analyzing machinery and its operation using industry-recognized methodologies. This information is known and kept by the machine’s OEM, the machine vendor, the system integrator, or the organization indicated by the machine safety risk assessments.
And just a friendly reminder, assembling your machine safety team and related documentation will require lots of collaboration. So be prepared to have several planning sessions, most likely, not just one.
Step Three: Review Documentation
Machine safety risk assessment and methodologies identify a performance level requirement, PLr. The PLr identifies the selection and design of any safety control solution for each machine safety risk, such as an interlock or a presence sensing device. Reviewing the machine’s operating instructions and maintenance requirements is critical to avoid oversight. For example, suppose your risk assessment is not identical to the actual machine operation? Meaning a validated machine safety solution was most likely not designed or engineered for this device.
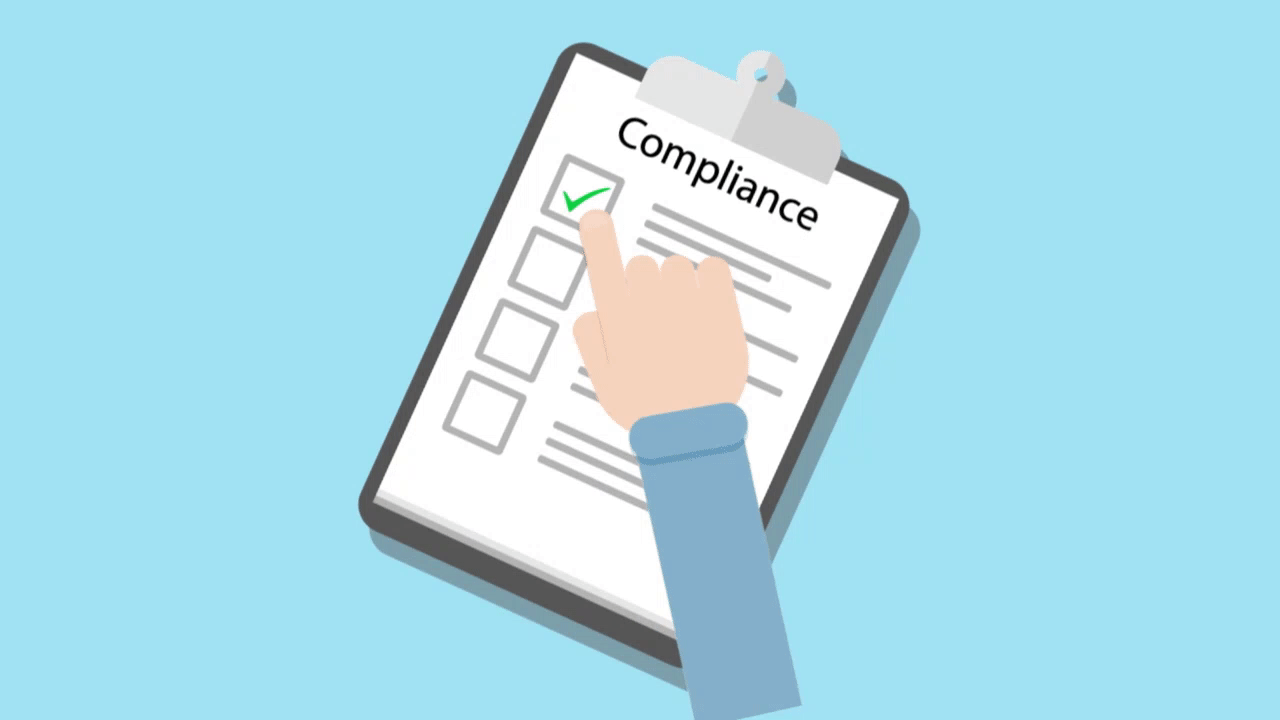
With the required PLr identified, you now need to review the selection of machine safety devices and components. First, find the technical machine file in the safety design and electrical and control schema file. Then, with the assistance of your in-house machine safety team and authorized lockout and tagout personnel observing your facility’s hazardous energy control procedures, you can confirm if the devices installed are as specified. If such devices are not present as outlined in the safety design or electrical cymatics, there should be serious doubts about the safety design or function of the machine.
If you experience this situation, you may want to stop your assessment internally, discuss the continued use of the device, and seek the assistance of qualified machine safety personnel.
Step Four: Review the Validation Documentation
These validation documents should indicate selections of the safety devices and components. These selections might include the method of configuration, wiring, and interruption type. With help from your in-house machine safety team, you may confirm if the control system validated the installed design. Also, if the required PLr was achieved for each installed device and configured to eliminate or reduce each machine safety hazard as indicated in the risk assessment to an acceptable level.
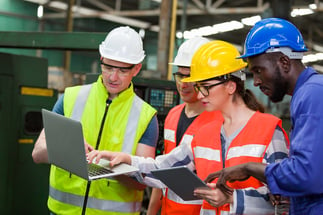
On the other hand, suppose there is no available validation documentation confirming ISO 13 849, gaps or uncertainties with the validation process, or unauthorized or undocumented safety device changes. In that case, there should be severe reasons to doubt the safety design and function of the machine.
If you experience this situation, you may want to stop your assessment internally, discuss the continued use of the device, and seek the assistance of qualified machine safety personnel.
Step Five: Seek The Assistance of Qualified Machine Safety Personnel
If all else fails, or if you have any questions or comments please do not hesitate to contact our MPSA machine safety experts!
Summary
To verify if your machine is safe and compliant, you’ll need to do the following.
-
-
-
1. Assemble and collaborate with your own in-house machine safety team
-
2. Collect essential documentation (such as machine operating instructions, risk assessments, safety design, and validation documentation)
-
3. Review documentation
-
4. If gaps or doubts develop, MPSA strongly recommends discussing the continued use of the device internally.
-
5. If all else fails, seek the assistance of qualified machine safety personnel.
-
-
Resources & Information
Watch the on-demand webinar: How do I know my machine is safe and compliant?
Updated Safety Standards & Regulations
Subscribe to our blog
Most Recent
Ensuring machine safety is a regulatory requirement and crucial to maintaining a safe and efficient working environment. The complexities of...
No matter the severity of the injury, whether it's a near miss, serious injury, or fatality, taking proactive measures can help prevent future SIF (...
It's that time of year when ghosts and goblins come out to play, and while we enjoy a good scare during the Halloween season, there's one thing that...
Safety must stand as an unwavering pillar in any laboratory setting, ensuring innovation thrives without compromising the well-being of those at the...
At your facilities, the utmost priority is the safety of your employees and the integrity of your operations. Every day, your machines are crucial in...
Ensuring the safety and well-being of employees operating industrial machinery requires a deliberate and well-designed approach. Applying “quick fixes
Did you know there's a crucial connection between machine safety maintenance and the well-being of your workers? It's true! And as technology...
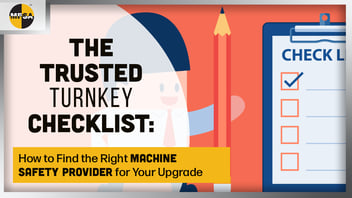
The Trusted Turnkey Checklist: How to Find the Right Machine Safety Provider for Your Upgrade Project
Here at MPSA, we define turnkey machine safety solutions as designed, built, installed, validated, and ready to operate. But finding a trusted...