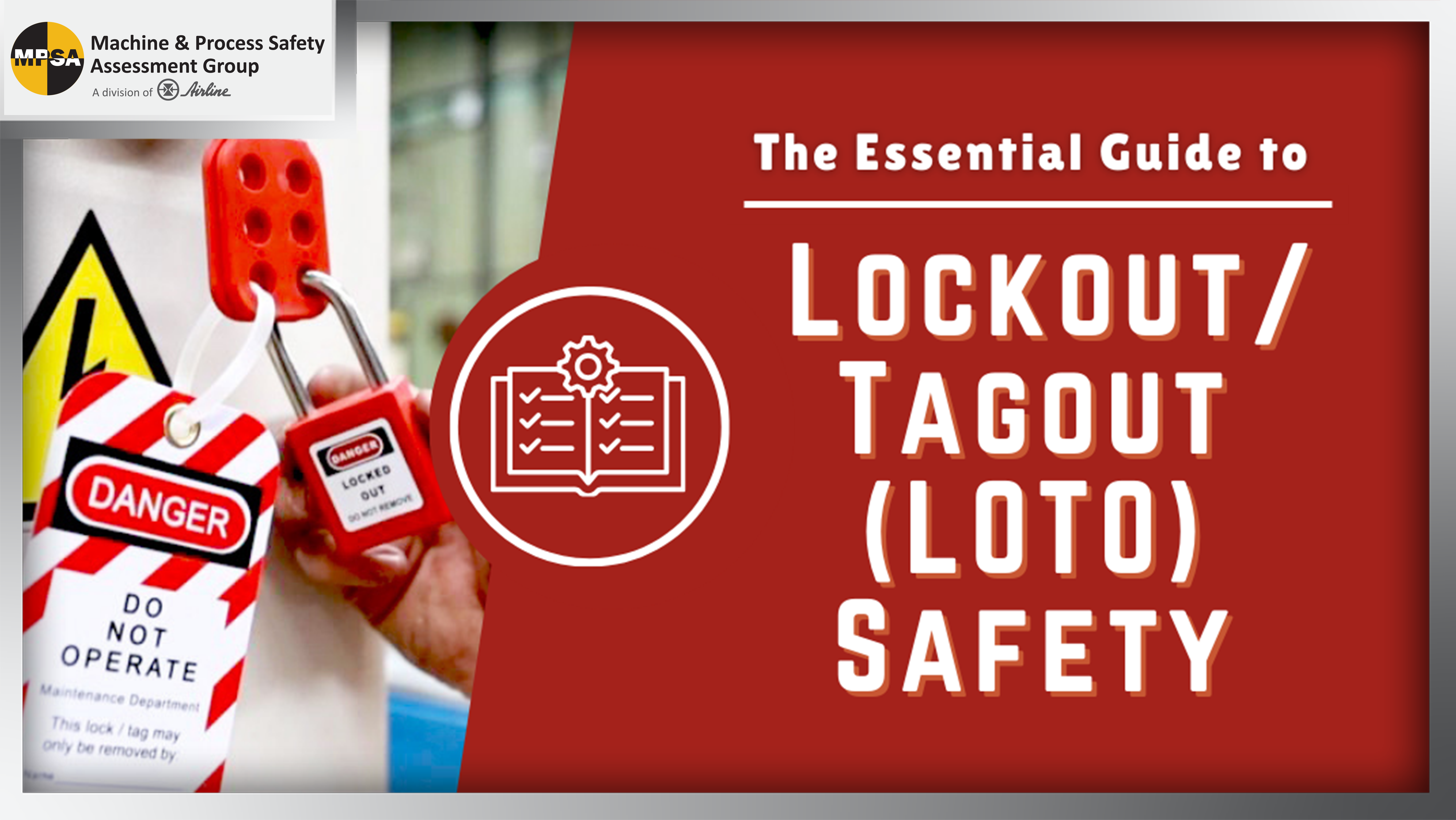
The Essential Guide to Lockout/Tagout (LOTO) Safety
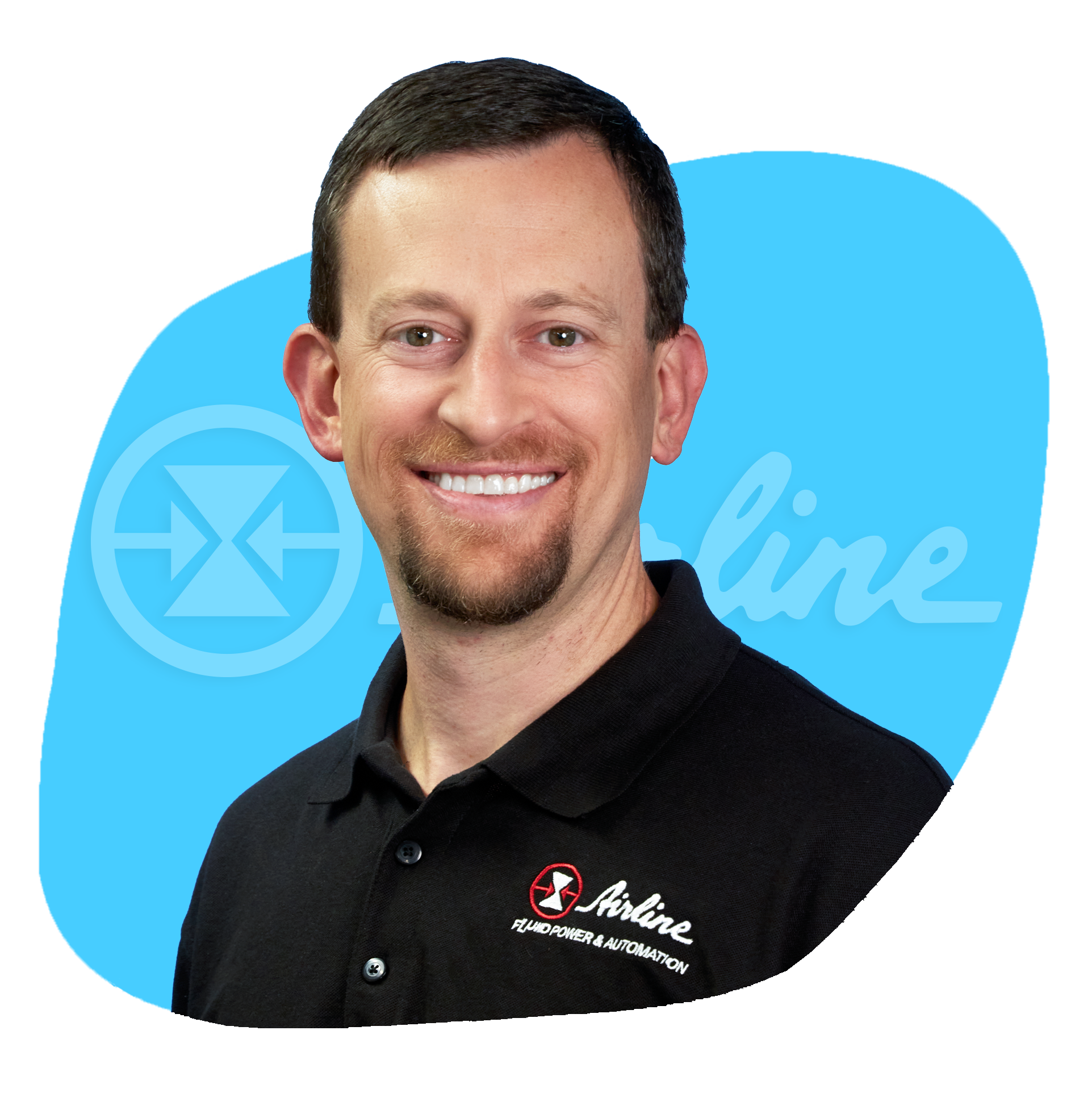
Posted By: Ryan Hayworth
June 29th, 2022
Imagine you're deep into a routine maintenance check, making sure every part of the machine is working smoothly and safely. Then, out of nowhere, the equipment jerks into motion. In a flash, you realize just how close you came to a dangerous incident—caught off guard by an unexpected start-up.
This is where Lockout/Tagout (LOTO) steps in, otherwise known as Hazardous Energy Control, a proactive measure designed to prevent the uncontrolled release of hazardous energies—including electrical, mechanical, hydraulic, pneumatic, chemical, and thermal—while maintenance and servicing activities are conducted.
In this guide, we'll explore the essential steps of LOTO, its key components, and how it aligns with OSHA standards, all while highlighting the significant benefits it offers. Let's walk through this vital process, ensuring safety and peace of mind for everyone involved.
In this Post
Lockout/ Tagout | Key Components | OSHA Regulations & Standards | Steps Implementing LOTO Procedures | Common Challenges | Products to Support Effective LOTO | Benefits of a Robust LOTO Program | Training and Awareness | Maintaining and Auditing | Additional Resources | Frequently Asked Questions
🎁 Request a FREE Sample of ChekVolt for LOTO
Key Takeaways Lockout/Tagout (LOTO) is essential for preventing accidents during maintenance by controlling hazardous energy in equipment. A successful LOTO program includes documented procedures tailored to specific equipment and requires regular training and audits for compliance. Adherence to OSHA regulations enhances safety and legal compliance, necessitating annual evaluations and proper implementation of LOTO procedures. Conformance to machine safety standards such as ANSI Z244.1 is essential for guidance in developing a proper hazardous energy control program. |
Understanding Lockout/Tagout (LOTO)
Keep reading or watch our YouTube video with ROSS Controls for a comprehensive review of LOTO.
Lockout/Tagout (LOTO) is a critical safety procedure designed to ensure that dangerous equipment is shut off and not restarted during maintenance. LOTO aims to protect workers servicing equipment from hazardous energy, which can lead to severe or fatal injuries if not controlled.
LOTO procedures include steps to prevent accidental equipment energization during maintenance, using lockout devices to physically prevent operation, and tagout devices to warn against it. These safety devices are essential in controlling hazardous energy and ensuring that equipment remains in a safe state throughout the maintenance process.
Following LOTO procedures is crucial. Without them, hazardous energy from machines can pose significant risks, leading to serious injuries or fatalities. The lockout device must be durable and distinct to ensure clear identification, while the tag indicates the responsible worker and the reason for the LOTO and contact information.
Key Components of a LOTO Program
When it’s time for machinery maintenance and repair, the first step is implementing the machine’s hazardous energy control procedures and your facility’s LOTO procedures.
For LOTO procedures to be effective and safe, Serious Injury Prevention (SIP) efforts must carefully evaluate the location and the adequacy of those devices provided for employees to identify, access, isolate, secure, and verify the status of each hazardous energy source.
But that's not all, a robust Lockout/Tagout (LOTO) program is built on several key components, each essential for ensuring the safety of workers during maintenance and repair activities. Here is an overview of each component:
Documented Energy Control Procedures:
- Employees must develop detailed instructions for managing hazardous energy.
- These procedures include steps for shutting down, isolating, and securing equipment.
- Employees must verify equipment isolation before maintenance.
- Ensure de-energization is complete to prevent accidents.
- Secure equipment from unintended energization.
- Lockout devices prevent operation; tagout devices serve as warnings.
OSHA Regulations and Standards for LOTO
Compliance with OSHA regulations is a fundamental aspect of any Lockout/Tagout program, so much so, it's estimated compliance with these standards deters an estimated 120 fatalities and 50,000 injuries each year. The OSHA standard for lockout/tagout is defined under 29 CFR 1910.147, which outlines the necessary actions for managing hazardous energy. These standards apply across various industries, including maritime and construction, ensuring that all sectors adhere to safe practices.
Additionally, ANSI/ASSP Z244.1 is a voluntary consensus standard that can be used for best practices and methods of hazardous energy control.
One of the key benefits of a LOTO program is compliance with safety regulations, which helps businesses adhere to legal requirements regarding workplace safety. OSHA mandates at a minimum, annual evaluations of LOTO procedures to ensure ongoing compliance and safety.
OSHA also requires Lockout Tagout training to protect employees working with potentially hazardous machinery. Adequate training of all personnel involved in LOTO procedures helps companies maintain high safety standards and prevent accidents.
Steps for Implementing LOTO Procedures
Upgrading and implementing Lockout/Tagout (LOTO) procedures can significantly enhance workplace safety. Here’s a streamlined approach to consider when assessing hazards and designing energy control procedures:
Key Considerations for Effective LOTO Upgrades
Accessibility
Ensure each hazardous energy source has labeled, accessible isolation devices located in safe, convenient spots. Ideally, position multiple isolation points together to simplify the process.
Isolation
Confirm that isolation devices, such as disconnect switches or dump valves, meet the necessary size and capacity to fully isolate each energy source. For hydraulic and pneumatic sources, check that the device includes an exhaust or bleed-down port to safely manage energy release.
Security
Verify that isolation devices can only be locked in the off/open position and are compatible with standard LOTO control tools, including padlocks, tags, and other securing hardware.
Verification
Check that each isolation device allows for clear and visible verification of a Zero Energy State (ZES), ensuring complete energy control before maintenance begins.
Implementing these upgrades reduces the risk of severe injury, boosts efficiency, and supports compliance with hazardous energy control standards.
LOTO Implementation Steps
With a clear understanding of the key considerations for effective LOTO upgrades, the next crucial step is to put these practices into action. Below, we'll outline the step-by-step process for successfully implementing LOTO procedures to ensure maximum safety during maintenance activities.
Notify Affected Employees
Inform everyone in the work area about the upcoming shutdown to prepare them for maintenance and prevent unintended exposure.
Identify Hazardous Energy
Determine the type and magnitude of all energy sources to control potential risks. Shutting down machines systematically minimizes hazards during maintenance.
Isolate and Secure Energy Sources
Disconnect equipment from energy sources using isolating devices. Lockout devices prevent accidental energy transfers, while tags signal that equipment is out of service until LOTO removal. Verify that residual energy is fully dissipated before starting maintenance.
Verify Isolation
Test the equipment to ensure all energy sources are isolated and controlled. This essential step confirms a Zero Energy State before beginning maintenance or repairs. As part of a comprehensive approach to testing, consider incorporating products like LOTO Voltage Indicators from Grace Technologies.
Restore and Re-energize Equipment
After maintenance, inspect and reassemble equipment as necessary, notify personnel, and then safely restore power.
Common Challenges in LOTO Implementation
Implementing a LOTO program is not without its challenges. One primary issue is failing to identify all sources of hazardous energy, which can lead to incomplete isolation and increased accident risk. Thoroughly assessing all potential energy sources is crucial to ensuring effective isolation.
To thoroughly assess all potential energy sources, conduct a comprehensive evaluation that includes identifying all energy types, measuring levels, analyzing the impact, and ensuring proper isolation methods are in place. Regular monitoring and updates to the assessment process are also essential to adapt to any changes.
Hazardous energy control devices can also be challenging to locate, as they are often not installed in convenient or accessible locations, hindering safe LOTO implementation. Additionally, shortcuts or gaps in LOTO procedures can increase the potential for severe injuries or fatalities.
Download our webinar to learn about hybrid machine safety solutions integrating electrical, electro-mechanical, and fluid power devices. You'll gain practical tools for holistic safety, helping you meet safety standards and reduce risks across your machinery. |
Products to Support Effective LOTO
A variety of products are available to support the effective implementation of LOTO procedures.
Key-retaining padlocks ensure that the key can only be removed after the lock is secured in place. Electrical lockout devices specifically secure the power supply to equipment, ensuring it remains in the ‘off’ state. Multi-purpose cable lockout devices allow for the simultaneous locking out of multiple energy isolation points.
Proper application and selection of LOTO devices are crucial. Color-coded locks and tags, although not standardized by OSHA, often include red for personal danger, orange for group isolation, and yellow for out-of-service situations. Tagout devices serve as visible warnings, indicating that equipment should not be operated during maintenance or repair.
A LOTO box is also useful for group lockout situations where several energy isolation points need to be secured at once. Shop all LOTO products on our website, www.airlinehyd.com.
Benefits of a Robust LOTO Program
A robust LOTO program offers numerous benefits, starting with a significant boost to workplace safety. LOTO procedures reduce the risk of severe injuries or fatalities during maintenance, protecting workers and creating a safer work environment.
A solid LOTO protocol also safeguards machinery, preventing costly damages from accidental activation. This translates to financial benefits, as implementing effective lockout/tagout procedures can prevent costly production delays related to unexpected equipment servicing.
A well-structured LOTO program enhances productivity by minimizing machine downtime during servicing. By minimizing workplace accidents through effective LOTO practices, businesses can maximize operational uptime and productivity.
Training and Awareness for LOTO Compliance
Comprehensive and role-specific LOTO training is essential for the success of any program. It helps workers understand risks, prevents violations, and ensures compliance. Employers are mandated to provide this training to ensure workers can effectively apply lockout/tagout procedures. The training includes the identification of energy sources, procedural application of devices, and emergency response protocols.
Annual refresher training is crucial to maintain proficiency and ensure ongoing compliance with safety standards. All workers in relevant areas must be informed about the purpose and usage of these practices.
Employers are tasked with developing an energy control program tailored to the workplace and equipment in use, while employees must receive training on these hazardous energy control procedures to ensure understanding and adherence.
|
Maintaining and Auditing Your LOTO Program
Regular audits and inspections maintain the effectiveness of a LOTO program. These inspections ensure that equipment remains properly secured and that safety protocols are followed. Regular reviews and audits of LOTO procedures help keep them updated and effective in addressing current safety risks.
Annual audits help identify and rectify gaps or deficiencies in lockout/tagout practices. Observing authorized employees during audits confirms they are correctly following lockout/tagout procedures.
Investing in lockout/tagout auditing software can also help manage and document the auditing process effectively. Streamlining the auditing process by dividing tasks among multiple auditors or scheduling audits quarterly can further enhance the effectiveness of your LOTO program.
Machine maintenance and repair always starts with LOTO. Unfortunately, shortcuts or gaps become commonplace without the correct safe, local, and complaint isolation devices, increasing the potential for severe, if not fatal, injuries. Take time to review these products and the ChekVolt Free Sample for ways to upgrade your LOTO program. These simple machine safety improvements may increase productivity and reduce turnaround times. |
Additional Resources
- Request a FREE Sample of ChekVolt for LOTO
- LOTO Training Resources
- Shop Machine Safety Projects
- OSHA LOTO Resources
- Updated Safety Standards & Regulations
- OSHA Standards Fact Sheet
Contact MPSA
If you have any questions or comments, please do not hesitate to contact MPSA machine safety experts!
Subscribe to our blog
Most Recent
Ensuring machine safety is a regulatory requirement and crucial to maintaining a safe and efficient working environment. The complexities of...
No matter the severity of the injury, whether it's a near miss, serious injury, or fatality, taking proactive measures can help prevent future SIF (...
It's that time of year when ghosts and goblins come out to play, and while we enjoy a good scare during the Halloween season, there's one thing that...
Safety must stand as an unwavering pillar in any laboratory setting, ensuring innovation thrives without compromising the well-being of those at the...
At your facilities, the utmost priority is the safety of your employees and the integrity of your operations. Every day, your machines are crucial in...
Ensuring the safety and well-being of employees operating industrial machinery requires a deliberate and well-designed approach. Applying “quick fixes
Did you know there's a crucial connection between machine safety maintenance and the well-being of your workers? It's true! And as technology...
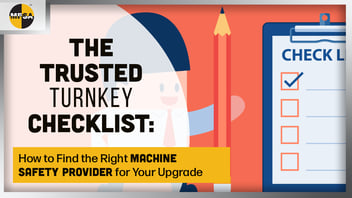
The Trusted Turnkey Checklist: How to Find the Right Machine Safety Provider for Your Upgrade Project
Here at MPSA, we define turnkey machine safety solutions as designed, built, installed, validated, and ready to operate. But finding a trusted...