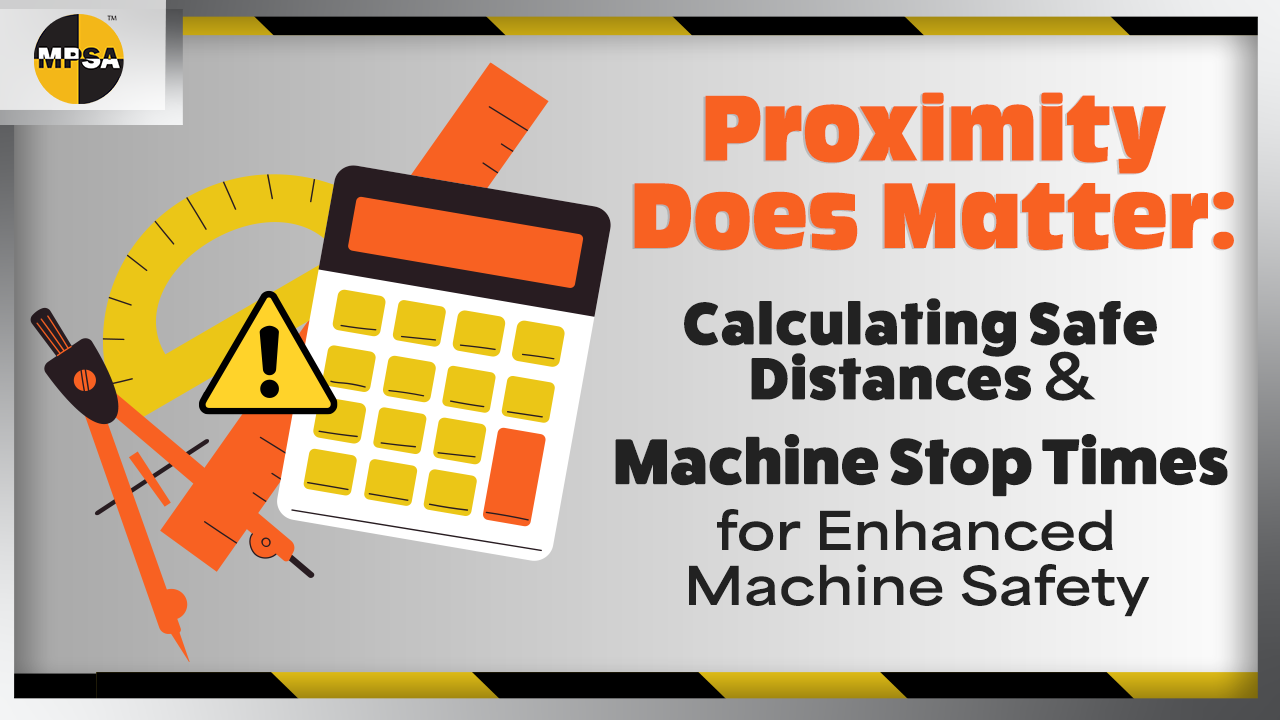
Proximity Does Matter: Calculating Safe Distances & Machine Stop Times for Enhanced Machine Safety
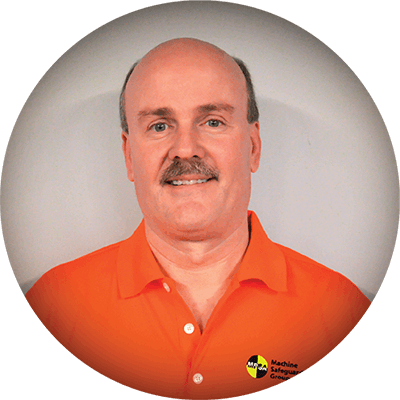
Posted By: David Kerr
July 20th, 2023
Ensuring the safety and well-being of employees operating industrial machinery requires a deliberate and well-designed approach. Applying “quick fixes” or waiting for a serious, if not fatal, injury before implementing machine safety improvements is simply not a complaint or sustainable approach. However, ensuring machine safety while meeting productivity, quality, and operational demands can be daunting, requiring careful consideration and expertise. So what are some of the solutions to consider? In this blog post, we will delve into the world of presence-sensing safety technology, exploring its importance in enhancing machine safety. We will also discuss the crucial process of calculating safe distances and machine stop times. By understanding the why and how behind these calculations, you can ensure a safer working environment for operators and increase overall machine efficiency.
Skip to a Section
Presence-Sensing Safety | Understanding the Need for Testing & Confirmation | Safe Distance Calculation Explained | Testing Machine Stop Times | Importance of Proximity in Calculating Safe Distances | Best Practices for Calculating Safe Distances | Summary
Presence-Sensing Safety
Often, one of the most intimidating challenges in dealing with industrial machinery arises when operators require access to a point of operation or need to reach or walk into the machine during regular production activities. Accessing this particular type of environment comes with its fair share of challenges. These challenges include safety risks, a lack of specialized training, a lack of communication between operators and human error, and so on. Nevertheless, presence-sensing safety technology (PSST) may be deemed appropriate in these situations.
This advanced safeguarding technology encompasses different components such as light curtains, pressure-sensitive floor mats, and area scanning devices. By utilizing PSST, these devices can effectively detect the presence of a person, a body part, or any foreign object within a specified area near or around the machine. When implemented correctly, this safety control technology enables the regulation of machine startup, motion, and stoppage upon detecting any unauthorized presence within the designated safe access zone.
However, before implementing this approach, it is essential to ascertain the machine's stop time, the response time of the chosen safety control device, and the available safety control and stop functions of the machine. Furthermore, a crucial step involves conducting a safe distance calculation to determine the required installation distance of the presence-sensing device from the hazardous point of operation, ensuring the suitability of this technology. Learn more about presence-sending technologies in our blog post, Guidelines for Safe-Distance Calculations & Presence-Sensing Devices.
Understanding the Need for Testing & Confirmation
Accurate machine stop time determination is absolutely critical when utilizing presence-sensing safety technology. By accurately determining machine stop times, you can provide employees with a compliant and robust safety solution addressing the operator’s access needs while mitigating the risks of injuries and increasing machine productivity, and efficiency of operations. Determining machine stop times can be a complex task and may require the use of specialized instrumentation and software. If your facility lacks expertise in determining machine stop time, you may want to consider contacting an experienced machine safety provider specializing in this field. MPSA is here to help - contact us!
Safe Distance Calculation Explained
S = K x (Ts + Tc + Tr + Tbm) + Dpf
Determining the safety distance calculation involves taking several factors into account. To make it easier to understand, let's break it down:
Firstly, the ANSI calculation method considers how fast a person or object approaches, how quickly the machine reacts, and how fast the safety devices respond. It also adds extra time to account for any differences in the machine's reaction time.
S: Safe distance - This is the desired minimum distance needed to be maintained to ensure the safety of anyone attempting access.
K: Safety factor - A constant accounting for additional safety margins or considerations specific to the application. It is typically greater than 1.
Ts: Stop time - The time needed for the machine or equipment to fully halt once the sensing device detects the presence of an approaching intrusion (person or object) encompasses both the deceleration and complete cessation of its motion. To determine the stopping time (Ts) of the machine, a standardized approach involves:
- Taking ten measurements of stop time.
- Calculating the average.
- Adding three times the standard deviation.
The highest value from those ten measurements is utilized in the calculation.
Tc: Control response time - The time the safety control system takes to respond once the sensing device detects the intrusion - this can include the time the control circuitry, relays, or other components takes.
Tr: Response time - The time it takes for the sensing device to detect the intrusion condition and send a signal to the safety control system, as well as the sensor's response time and any delays in signal transmission.
Tbm: Blanking time - When the sensing device ignores certain objects or movements. It is typically used to prevent false triggers from non-hazardous conditions, like brief reflections or temporary obstructions.
Dpf: Dynamic protective field - This represents the extra distance required to account for the movement or reach of individuals within the protected area. It ensures even if someone reaches into the hazardous area, they remain outside the danger zone.
By multiplying the sum of Ts, Tc, Tr, and Tbm by the safety factor K and adding the dynamic protective field distance Dpf, the formula calculates the overall safe distance S required for the light curtain or sensing device in a particular application. It's worth noting that the specific values for Ts, Tc, Tr, Tbm, K, and Dpf will depend on the specific application, the characteristics of the equipment or machinery involved, and the relevant safety standards and regulations. These values must be determined based on a machine safety risk assessment, manufacturer specifications, applicable regulatory requirements, and industry-recognized standards and guidelines.
By carefully considering these factors and employing the appropriate formulas and requirements, you can accurately calculate the safety distance required to safeguard employees from accessing hazards on industrial machinery.
Testing Machine Stop Times: Real World Example
Testing and confirming machine stop times is critical to ensuring machine safety in any industrial setting. Imagine a high-speed testing machine that evaluates the strength of various materials by subjecting them to extreme forces. A machine of this nature cannot instantly come to a complete stop once the operator activates a stop mechanism. It requires a certain amount of time for the machine to respond to the safety device and all interconnected components before it can achieve a complete stop. If, for instance, the presence-sensing safety device, acting as a safeguarding device, is positioned too close to the testing area, the machine may not have sufficient time to react and halt its operations before an operator or a body part can enter the hazardous zone.
Another important consideration with some industrial machinery is coast-down time, which refers to the duration it takes for the machine's moving parts to come to a complete stop after the primary process is halted or a stop mechanism is activated. This coast-down time is often due to inertia and is necessary to prevent damage to the machine or its products. Employing guard-locking interlocks in such situations may be a more suitable solution. These interlocks keep the protective guards securely locked, physically denying access to personnel until all hazardous motions have entirely ceased.
Importance of Proximity in Calculating Safe Distances
Knowing the accurate machine stop time and then calculating the safe distance for the installation is absolutely crucial for the safe and compliant use of presence-sensing safety technology. These safe distances consider factors such as the equipment's speed, force, and motion, as well as the reaction time of the safeguarding devices. By adhering to these calculated safe distances, workers are provided with a buffer zone that mitigates the likelihood of contact with the hazardous machine part and reduces the chance of injury.
Best Practices for Calculating Safe Distances
Familiarize Yourself with Applicable Regulations and Standards:
Understand the relevant local or national regulatory requirements and industry-specific standards for your machinery. Examples include the United States OSHA (Occupational Safety and Health Administration), ANSI (American National Standards Institute) and ISO (International Organization for Standardization).
Document and Communicate Results:
Maintaining comprehensive documentation for any presence-sensing safety device utilized within your facility is important. These documents must be readily accessible in the event of inspections by regulatory agencies, internal audits, or other forms of inspection. They serve as your facility's records, demonstrating the safe and compliant installation of presence-sensing safety devices. Your records should encompass the following details for each presence-sensing safety device:
- Device specifications
- Determinations of machine stop time
- Calculations of safe distances
- Installation specifications
- Safety control schematics
- Testing documentation
- Change control documentation
These documents should be made available to relevant stakeholders, including production management, machine operators, maintenance personnel, instrumentation/automation personnel, and EHS personnel.
Periodic Review and Update:
As time passes, the demands for production or quality tend to change, requiring adjustments or alterations to machinery and operational circumstances. Regularly reviewing and confirming the installed location of the device, the operator's access point, machine stop times, and safe distance calculations are essential to ensure the ongoing effectiveness and compliance of proximity-sensing safety devices. The ongoing use of presence-sensing safety devices must be maintained strictly with your site’s Management of Change (MOC) or Mechanical Integrity procedures.
Operator & Maintenance Training:
Ensure your employees are trained on how presence-sensing safety technology and devices work, any device limitations, and the documented safe distance equations that apply. Train employees to recognize and report any operational deviations, near-misses or close calls and strict conformance to the exact placement of the device based on the safe distance equations. Conduct periodic audits, inspections, and conversations with machine operators to learn of any unreported events and confirm that devices have not been modified or relocated without the calculated safe distance approved through your site’s Management of Change (MOC) procedure.
Engage Qualified Experts:
If your facility lacks in-house machine safety expertise, consider contacting an experienced machine safety provider specializing in this field. Their knowledge and experience can ensure proper safety device selection, determination of machine stop times, safe-distance calculations, proper device installation, and compliance with applicable regulatory regulations and industry standards.
Summary
By incorporating presence-sensing safety technology, conducting precise safe-distance calculations, and implementing regular inspections and training, you can effectively safeguard employees who have access to point-of-operation hazards or reach-in areas.
Understanding the rationale and methodology behind these calculations will not only create a safer working environment for operators but also enhance overall machine efficiency.
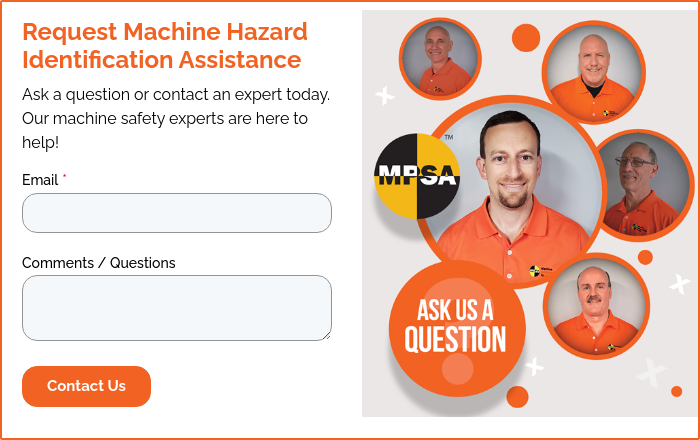
Machine Safety Resources
- MPSA Website
- Machine Safety Standards & Regulations
- Meet the Team
- Guidelines for Safe-Distance Calculations & Presence-Sensing Devices
- Machine Safety Webinars
- MPSA Services
Subscribe to our blog
Most Recent
Ensuring machine safety is a regulatory requirement and crucial to maintaining a safe and efficient working environment. The complexities of...
No matter the severity of the injury, whether it's a near miss, serious injury, or fatality, taking proactive measures can help prevent future SIF (...
It's that time of year when ghosts and goblins come out to play, and while we enjoy a good scare during the Halloween season, there's one thing that...
Safety must stand as an unwavering pillar in any laboratory setting, ensuring innovation thrives without compromising the well-being of those at the...
At your facilities, the utmost priority is the safety of your employees and the integrity of your operations. Every day, your machines are crucial in...
Ensuring the safety and well-being of employees operating industrial machinery requires a deliberate and well-designed approach. Applying “quick fixes
Did you know there's a crucial connection between machine safety maintenance and the well-being of your workers? It's true! And as technology...
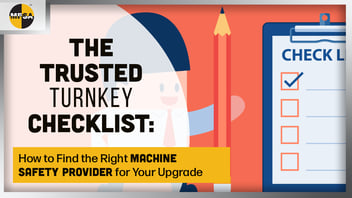
The Trusted Turnkey Checklist: How to Find the Right Machine Safety Provider for Your Upgrade Project
Here at MPSA, we define turnkey machine safety solutions as designed, built, installed, validated, and ready to operate. But finding a trusted...