Safety Risk Assessments
Mitigate risks, achieve compliance, and enhance production
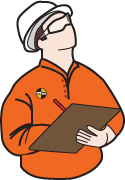
At MPSA, we understand that safety is paramount in the manufacturing industry. Our Machine Safety Risk Assessments are designed to provide an in-depth, systematic evaluation of your machinery's safety hazards, ensuring compliance with all relevant safety standards and regulations. Whether you are introducing new machines or seeking to enhance the safety of existing ones, our certified safety consultants are here to help.
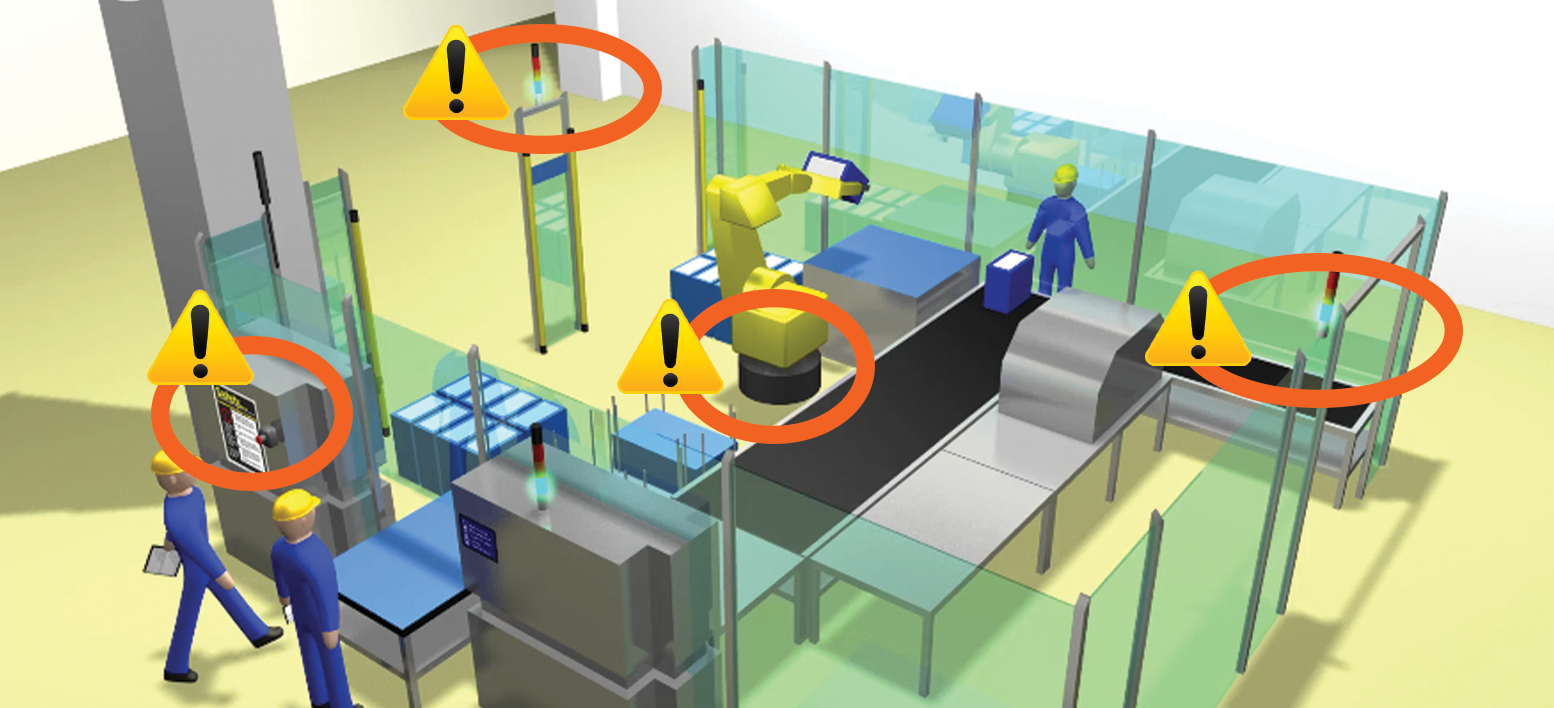
Comprehensive Safety Analysis
During the risk assessment, a certified safety consultant thoroughly measures safety hazards and their severity, exposure, and probability with a safety risk assessment. Then, based on facility input, MPSA will rate the frequency, severity, and level of avoidance for each risk. A decision tree is then used to determine the absolute risk of the machine (based on ANSI-B11) or for each safety function (based on ISO 13849).
The certified safety consultant will identify points of hazard during all potential conditions of machine use. They will also evaluate the probability of injury, severity level, and the actual or potential exposure of all workers. They will communicate safety risk findings throughout the entire process and will work together to prioritize solutions for the most severe safety risks.
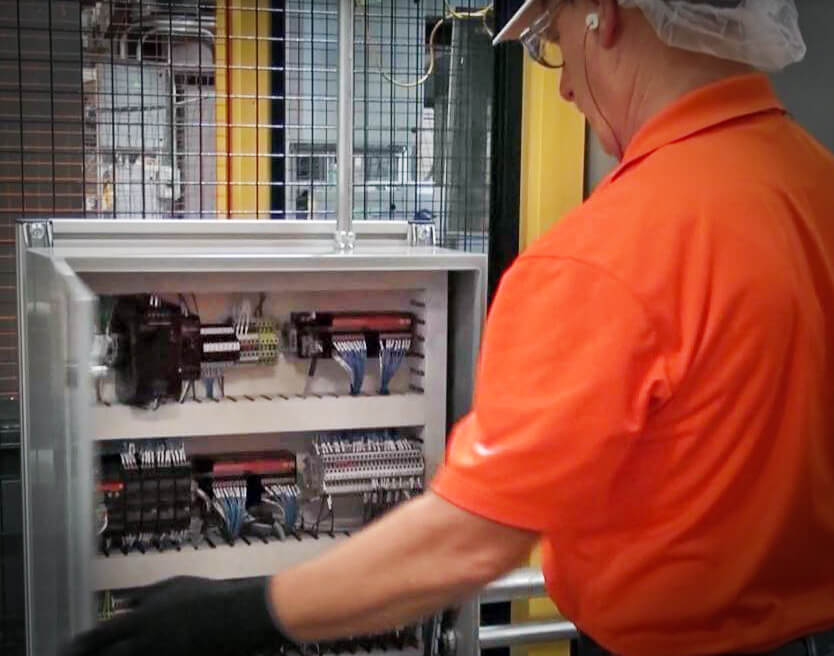
MPSA's Risk Assessment Will:
- Identify Points of Hazard during all potential conditions of machine use.
- Evaluate the Probability of Injury, Severity Level, and the actual or potential exposure of all workers.
- Communicate Safety Risk Findings throughout the entire process.
- Prioritize Solutions for the most severe safety risks.
Rigorous and Detailed Evaluation
Our Machine Safety Risk Assessment involves:
- In-Depth Evaluation covering approximately one day per machine, including all routine tasks such as operation, setup, adjustments, retooling, and maintenance.
- Rigorous Compliance conforming to ISO-12100, ANSI B11.0, and RIA TR 15 risk assessment standards, meeting OSHA requirements.
- Inclusive Engagement involving all impacted parties including machine operators, mechanics, cleaners, facility automation/instrumentation, and EHS teams.
- Document & Training Assessment where we will review and evaluate all equipment usage documentation, including equipment and training manuals and maintenance logs. We will also examine the process used to determine operator training, outlining evaluations.
- Control Reliability Assessment to identify the non-mechanical hazards that affect the control reliability of the machine. Control reliability and non-mechanical risks pertain to the electrical, pneumatic, and hydraulic components and circuits and their operations
-
Procedural Assessment, where we'll review and evaluate the methods and procedures used in the processing, use, handling, or storage of materials, tools, and substances used in your application.
Risk Prioritization Matrix
By estimating the length of exposure to the hazard and assessing the worst injury possible, the risk prioritization matrix can be used to determine the level of threat from each hazard that has been identified. Prioritizing hazards can prepare you to correct the most dangerous situations first and make plans to correct lower-ranking hazards in the future.
Rigorous and Detailed Evaluation
After completing the assessment, you will receive:
- In-Depth Evaluation covering approximately one day per machine, including all routine tasks such as operation, setup, adjustments, retooling, and maintenance.
- Rigorous Compliance conforming to ISO-12100, ANSI B11.0, and RIA TR 15 risk assessment standards, meeting OSHA requirements.
- Inclusive Engagement involving all impacted parties including machine operators, mechanics, cleaners, facility automation/instrumentation, and EHS teams.
- Document & Training Assessment where we will review and evaluate all equipment usage documentation, including equipment and training manuals and maintenance logs. We will also examine the process used to determine operator training, outlining evaluations.
- Control Reliability Assessment to identify the non-mechanical hazards that affect the control reliability of the machine. Control reliability and non-mechanical risks pertain to the electrical, pneumatic, and hydraulic components and circuits and their operations
-
Procedural Assessment, where we'll review and evaluate the methods and procedures used in the processing, use, handling, or storage of materials, tools, and substances used in your application.
Key Deliverables for Advancing Concrete Safety Initiatives
After completing the assessment, you will receive:
Risk Assessment Results Report
The detailed machine safety assessment findings are presented in an Excel file
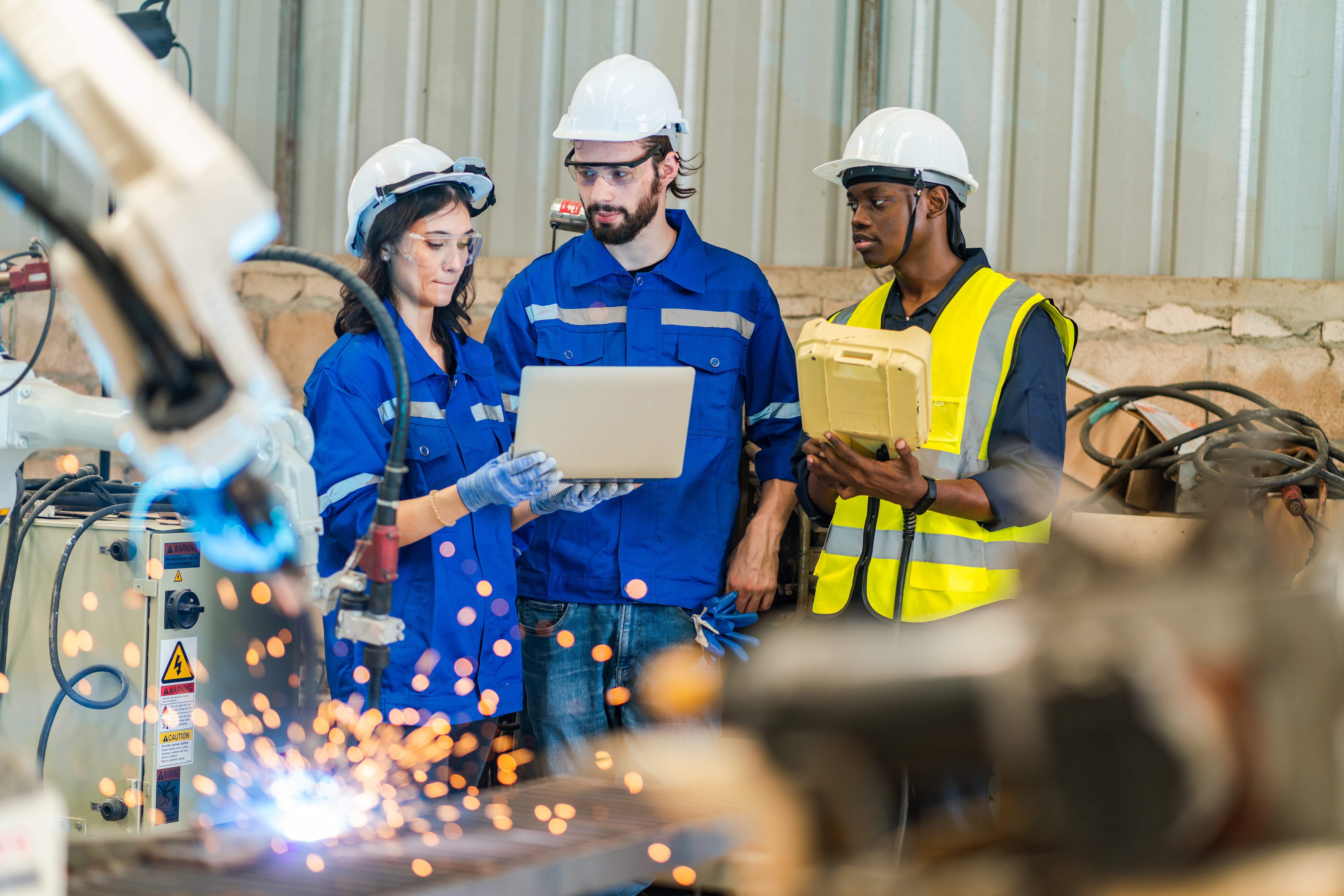
You will receive industry-accepted safety recommendations to eliminate or reduce the mechanical hazards that have been identified. Learn more.
Budget Estimate for Solutions
Budgetary cost estimates for proposed safety solutions (+/—25%).
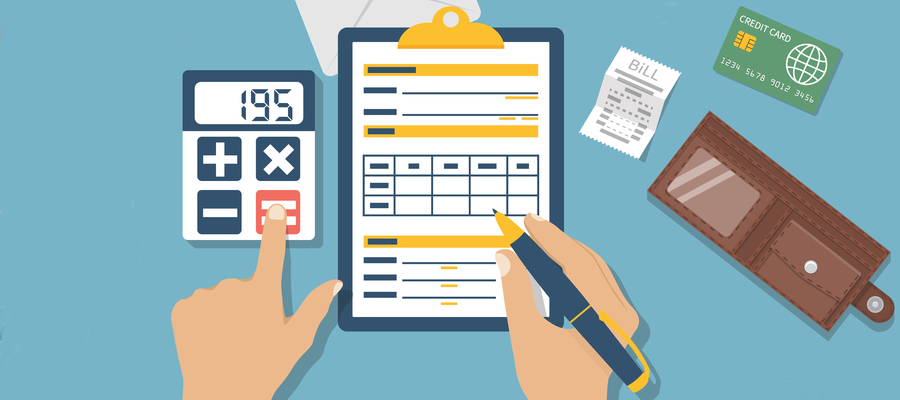
Need more detailed deliverables with fixed pricing?
📝 Explore Risk Assessment with Detailed Scope
Comparison Table for MPSA's Hazard Assessments
Unsure what hazard assessment suits your needs?
This guide will help you compare and contrast MPSA's three machine hazard assessment options.
Safety Surveys |
Risk Assessments |
Risk Assessments with Detailed Scope |
|
Level of Analysis | Overview | In-Depth | In-Depth |
Time Required | 1 hour/machine | 1 day/machine | 1 day/machine |
Operational Disruption | Minimal | Moderate | Moderate |
Compliance Standards | OSHA, ANSI | OSHA, ANSI, ISO-12100, ANSI B11.0, RIA TR 15 | OSHA, ANSI, ISO-12100, ANSI B11.0, RIA TR 15 |
Deliverables | Survey Results Report, Recommendation Report, Budget Estimate | Risk Assessment Results Report, Recommendation Report, Budget Estimate | Risk Assessment Results Report, Recommendation Report, Visual Aids, Conceptual Layouts, Safety Control Scope, Fixed Price Proposal |
Expertise Conducted by Certified Machine Safety Experts (CMSE), Licensed Machine Safety Specialists (LMSS), or Certified TÜV Functional Safety Engineers |
✔ | ✔ | ✔ |
Risk Prioritization | Numerical scoring system to prioritize improvements | Risk prioritization matrix | Risk prioritization matrix |
Cost Efficiency | High | Moderate | Moderate |
Inclusiveness The level of participation required from the client's personnel |
Basic input from machine operators | Detailed input from operators, mechanics, cleaners, EHS teams & other stakeholders | Detailed input from operators, mechanics, cleaners, EHS teams & other stakeholders |
Documentation Preparation The level of documentation required from the client on their machines/processes |
Limited | Detailed | Detailed |
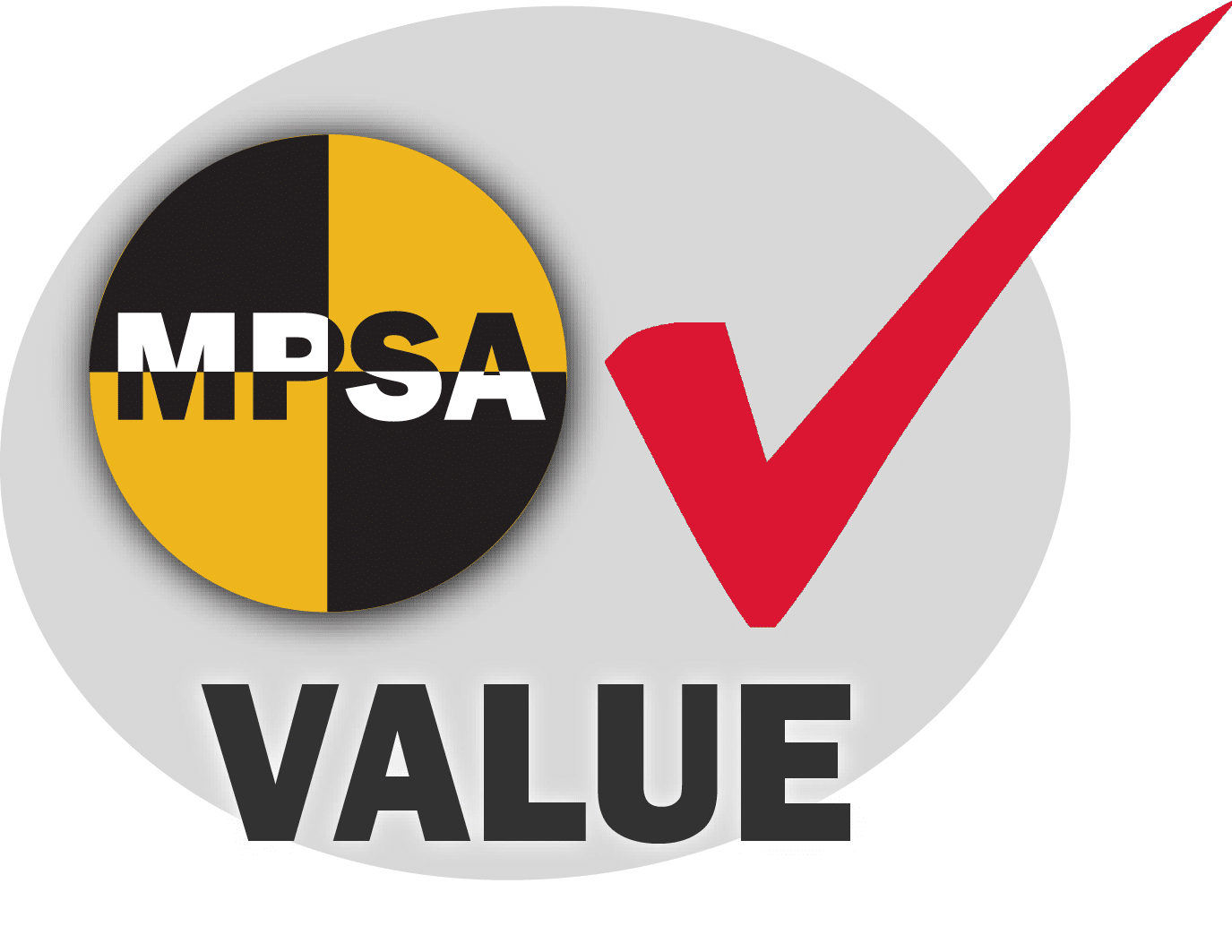
Discover the MPSA Advantage
With any of MPSA's Machine Safety Hazard Assessments, you gain more than just an evaluation. You gain a partner dedicated to enhancing every aspect of your machine safety management. Experience the MPSA advantage today and ensure your facility meets the highest safety standards.
Ready to take the next step? Schedule a free consultation to discuss your Machine Safety Risk Assessment needs and secure the safety of your workplace.
Schedule a Risk-Free Machine Safety Consultation
Schedule a consultation directly with MPSA's Application Engineer, Ryan Hayworth
Or submit our contact form to get started
More Hazard Assessments from MPSA
MPSA offers three types scalable to your needs:
Safety Surveys
Quickly & cost-effectively identify machine safety risks & which machines are most hazardous
Risk Assessment
Risk Assessment & Detailed Scope
MPSA’s Machine Safety Survey is the simplest and most cost-effective way to identify hazards.
Have a machine safety concern? Tell us about it!
Ask a Quick Question
Ask a quick question about machine guarding or MPSA.
Contact an Expert
Ask an in-depth question or start a discussion with one of our safety experts.
Request a Hazard Assessment
Request an MPSA professional on-site visit to identify hazards in your machinery and processes.